However, due to the large difference in thermal physical properties such as the melting point and thermal expansion coefficient of the two metals of steel and aluminum, and the low solid solubility between the two metals, the weldability of dissimilar metals of steel and aluminum is very poor. There is a large residual stress, and defects such as deformation and micro-cracks are prone to appear in the weld, and it is sensitive to stress corrosion. Especially in the welding process, brittle intermetallic compound layers are easily produced in the joints, which severely limits the further application of steel/aluminum composite structures. How to suppress the formation of brittle intermetallic compounds at the interface during the welding of steel/aluminum joints is a key issue in obtaining high-quality welded joints.
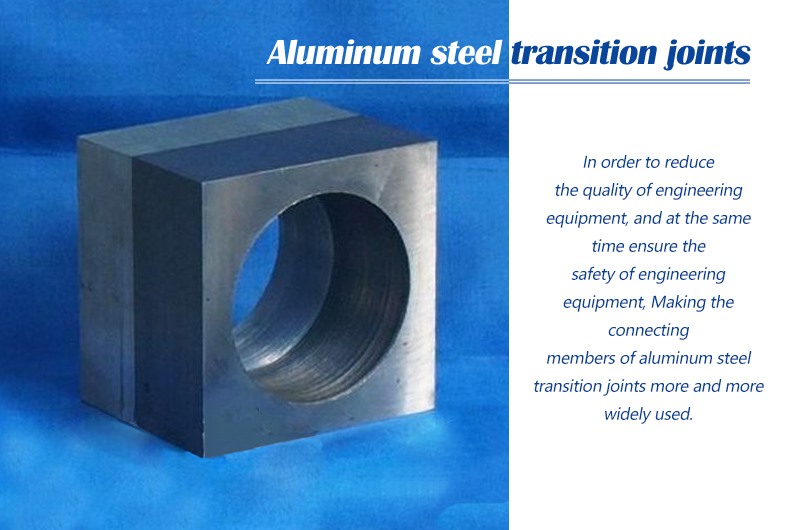
When using traditional fusion welding methods to weld aluminum-Steel electric transition joints, the heat input is too high. The two materials are directly fused to form a large amount of intermetallic compounds, which seriously deteriorates the mechanical properties of the joints; solid-phase welding methods can obtain higher-quality dissimilar metals However, the cost is higher, the shape of the joint is more restricted, and the welding efficiency is lower; the joint strength obtained by brazing technology is generally lower, and it has greater limitations for the welding of larger-sized and complex-structured components. The welding and brazing technology, which has the dual characteristics of welding and brazing, is an ideal welding method for the aluminum-Steel electric transition joints. During the brazing process, the high-melting-point base metal basically remains solid, and only the low-melting-point base metal is melted to form a welded joint by wetting and spreading on its surface.
In this way, the liquid phase mixing of dissimilar metals can be avoided, and the size of the interface compound layer can be effectively controlled, thereby improving the quality of the joint. Fusion brazing also overcomes the limitations of solid phase welding and brazing in terms of structural adaptability, welding efficiency and joint strength. However, the use of arc as the heat source for fusion brazing needs to overcome many problems, such as low energy density, large heat input, and insufficient control of interface reactions. The use of laser as the heat source of fusion brazing can achieve extremely fast heating and cooling speeds, accurately control the welding heat input and heating area, and has a great advantage in inhibiting the growth of the interface brittle reaction layer, which is a high-efficiency and high-quality welding of dissimilar species. Metal materials provide a valuable new idea. To this end, this article will use the laser deep penetration brazing method to conduct welding experiments on butt-joined steel/aluminum composite joints under different process parameters to study the essential factors affecting weld formation, interfacial reaction, and joint mechanical properties.