The anode on the pre-baked tank is replaced with a new anode after a certain period of use, and the part that is not consumed is the residual anode. These residual anodes are returned to the anode production system after steel claw detachment, electrolyte cleaning, and carbon block crushing treatment. The return residual electrode has a certain influence on the mechanical strength, air reactivity residual and carbon dioxide reactivity residual of the prebaked anode. Appropriate pre-baked anodes with residual electrodes have a good effect on reducing anode production costs, improving anode mechanical properties, and stabilizing anode production quality. The quality of prebaked anodes with high quality residues is better than that of prebaked anodes with low content or no residues. However, in actual production, the aluminum electrolytic carbon enterprises that digest the residual electrode have more electrolyte residues on the surface of the residual electrode during the cleaning, stacking, crushing, self-grinding and other processes due to the restrictive factors in all aspects of production, and the cleaning is not clean. After crushing, the electrolyte is directly fed into the prebaked anode production system in the form of ash.
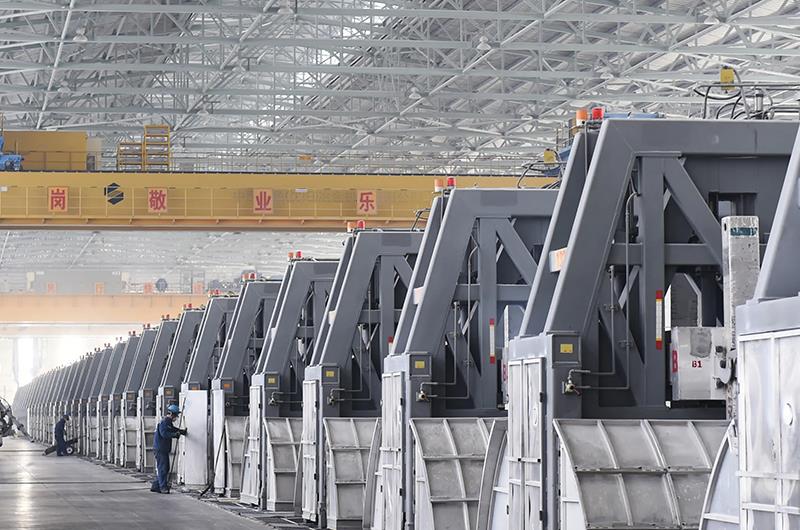
How to reduce ash in residual anode?
In order to reduce the ash content in the residual pole, each enterprise adopts different measures to control the residual pole ash content according to the actual situation, mainly including manual cleaning with steel brush, small particle residual pole efflux and experimental research on residual pole block self-grinding and other measures to reduce the residual pole ash content. Ash in the residue. At present, the aluminum electrolysis plants that return to the residual electrode are mainly realized by controlling the amount of the residual electrode, strengthening the cleaning of the residual electrode, and using some new technology and equipment.
1. Use residual pole shot blasting, this method can solve part of the problem of residual pole surface cleaning, but the amount of steel grit used in this equipment is relatively large, and the cost of steel grit alone increases by more than 100,000 yuan per month, and requires special Operators operate, equipment maintenance workload is heavy, equipment failures occur frequently, operating costs are high, and they are not put into use in actual production.
2. Treat with chain sling and wire brush, that is, add chain sling and wire brush to treat the surface of the suspended residual pole before the residual pole is separated from the steel claws. This method is not good for cleaning the bottom of the residual pole. It caused a lot of dust inside, and the environment was very harsh. Many manufacturers without special dust removal had to give up this measure.
3. Improve the screening treatment of the production process, improve the raw anode production line, and screen the residual electrode below Φ1mm after the residual electrode is crushed, so that the Φ1mm residual electrode in production does not enter the production batching system; specific optimization The process method is as follows: the large particle residual material is directly mixed into the production line; the granular material after classification by the vibrating screen is made a special channel, a filling silo is built to hold the granular material of Φ1-6mm, and a screw conveyor is installed to transfer the granular material. The material is transported to the outside pipeline and directly to the new silo, and the powder with the small particle residue below Φ1mm is directly discharged into the dust silo.
In view of the problems existing in the equipment and methods for cleaning the residual electrode, firstly pass the industrial tests such as shot blasting machine and steel brush cleaning on site, combined with the actual layout of the existing production line process equipment, replace the screen at the bottom of the vibrating screen, and remove the residual electrode below 1mm. The powder discharge can realize the automatic separation of online residual electrode powder, effectively solve the environmental problems caused by other residual electrode cleaning methods, and lay a good raw material foundation for producing high-quality pre-baked anodes and improving the economic and technical indicators of aluminum electrolysis.