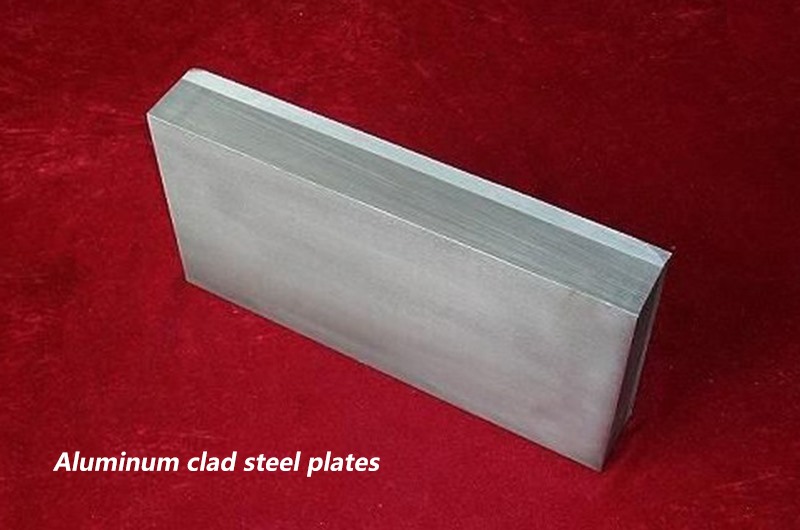
In the laboratory, the warm-rolled composite experiment and the interface shear strength test of steel/aluminum composite plates of different thicknesses were carried out. In order to avoid the oxidation of the interface of the steel/aluminum composite billet during the preheating process, the slab is covered with aluminum foil under the protection of inert gas to achieve a good expected effect. Under the working conditions of the original layer thickness ratio of 1:1, the rolling temperature of 400℃, the rolling speed of 60mm/s, and the single pass reduction rate of 40%, the four-sided thicknesses of 1.5mm, 2mm, 3mm, 4mmm were carried out. Rolling experiments of steel/aluminum composite plates with different thicknesses. The results show that the interfacial shear strength of the steel/aluminum composite plate shows a changing law that decreases with the increase of the component thickness. When the initial single-sided component thickness is 1.5mm, the average interfacial bonding strength of the composite board is 62MPa; when the initial single-sided component thickness is 4mm, the average interfacial shear strength of the composite board drops to 21MPa, which can no longer achieve effective composite . At the same time, advanced equipment such as scanning electron microscope (SEM) and energy spectrometer (EDS) was used to observe and analyze the microscopic morphology and element diffusion of the steel/aluminum composite interface under different working conditions.