Anodes are large carbon blocks that conduct electricity during the reduction of aluminum.
The anode conducts electricity and is therefore consumed at a rate of about 450 kg/tonne of aluminium. At present, two smelting processes coexist, one is self-baking process and the other is pre-baking process, the main difference is the difference of the anode used.
Self-baking electrolytic aluminum plants use continuously generated anodes, that is, continuous addition of bitumen to the top of the electrolytic cell. The heat generated by the reduction reaction roasts the pitch into the charcoal needed for alumina reduction, so that the waste energy in the electrolyzer can be utilized.
The pre-baking technology uses anodes that have been baked in a large, high-temperature gas furnace. Once the anode is exhausted, it needs to be replaced with a new one. Compared with self-baking technology, pre-baking technology has the advantages of high efficiency and less environmental pollution.
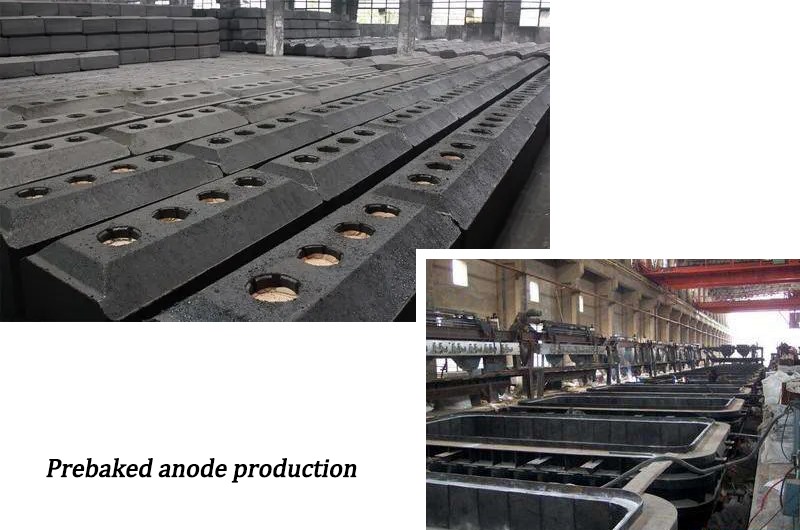
Prebaked anode production process
Prebaked anodes are produced in the anode workshop of electrolytic aluminum plants. The raw materials include petroleum coke, pitch, and residual anodes recovered from the electrolysis workshop (the part that remains after the anode is used). These ingredients are mixed together, heated, and poured into molds. Once formed, these anodes are sent to a "baking chamber".
In the bake shop, the formed anodes are placed in a furnace and heated at a temperature of 1120°C for approximately two weeks. By firing, the anode becomes a hard, uniform carbon block that can withstand the extreme conditions inside the electrolyzer while ensuring conductivity and smooth anode consumption.
The final stage of anode production is in the "steel rod installation room". Here, molten cast iron is used to weld the carbon block to a steel rod (through which the carbon block can be placed in the electrolytic cell, and the steel rod can also conduct electricity). The anodes with the steel rods are then sent to the electrolysis workshop, where they are installed in the electrolysis cells.
Instructions for use of prebaked anode
The pre-baked carbon anode is usually installed on the upper part of the electrolytic cell, and a strong DC current of 60-300ka passes through the carbon anode and introduces the electrolyte. The resistivity of the carbon anode is 50-70 μΩ.m, plus the guide rod and contact resistance, the voltage drop on the consumed carbon anode during normal aluminum electrolysis production is 300-500mV, accounting for 10%-15% of the voltage drop of the electrolytic cell %. At the point where the bottom of the carbon anode contacts the molten electrolyte, a complex electrochemical reaction (anodic reaction) that decomposes alumina occurs. With the participation of carbon, the anode end products are CO and CO2. In the production of aluminum electrolysis, the average daily consumption of carbon anodes is 1-2CM. Regularly adding new anode paste to the upper part of the electrolytic cell (for self-baking anode electrolytic cells) or regularly replacing pre-baked anodes (for pre-baked anode electrolytic cells) is the anode work. The main content to keep the anode continuously working properly.