With the rapid development of aluminum electrolysis technology, the anode used in electrolytic aluminum has also transitioned from self-baking anode to pre-baked anode, and the pre-baked anode carbon block group is composed of three parts with different materials: aluminum guide rod, cast iron Steel claw head and calcined anode carbon block. They are connected together by welding (between the guide rod and the cast steel claw) and phosphorus pig iron casting.
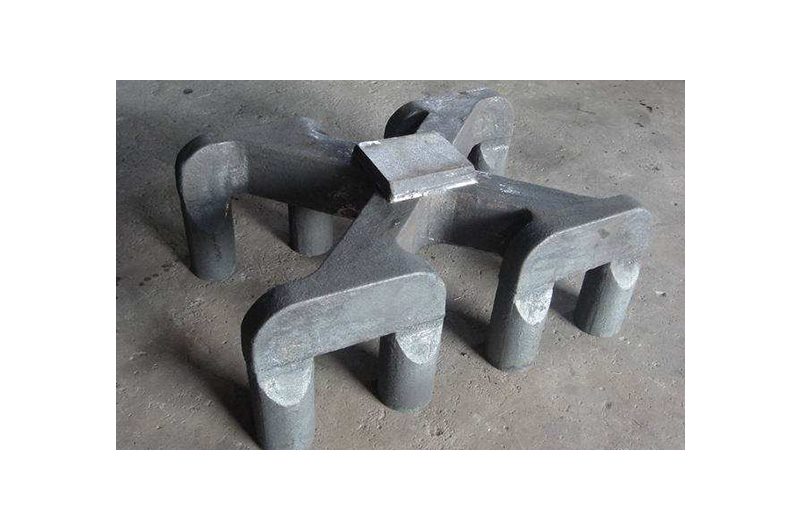
Process of Prebaked Anode Steel Claws for Electrolytic Aluminum
In order to facilitate the iron ring on the steel claw to be easily pressed off, it is necessary to dip the 120mm high graphite liquid on the steel claw head before casting. The original graphite liquid is prepared with 60% kerosene, 20% hydraulic oil and 20% graphite powder. Compressed air is introduced into the graphite liquid tank for stirring. When the anode guide rod and the steel claw are directly above the graphite liquid tank, the graphite liquid tank moves upward under the action of the cylinder, so that the steel claw claw head is stained with graphite liquid.
The original graphite liquid tank is improved, the air stirring is cancelled, the nozzle of the original compressed air is blocked, a cylinder is installed in the length direction of the graphite liquid tank, and a stirring device is designed at the front end of the piston rod. When it is directly above the graphite groove, the graphite groove rises, and after the graphite powder in the graphite groove submerges the steel claw head, the steel claw is stained with graphite powder, the graphite groove descends, and the guide rod is discharged. Due to the large cross-section of the steel claws (Φ160mm), the graphite powder is easy to agglomerate after dipping a few steel claws, so it is necessary to stir the graphite powder, so it is set in the program that after dipping 5 steel claws, it will automatically stir back and forth. once.
Advantages of Process of Prebaked Anode Steel Claws for Electrolytic Aluminum
Before dipping the graphite powder, a thin layer of carbon powder is attached to the surface of the steel claws. The resistance of the iron ring is reduced, and the iron ring is easily pressed off.
After the dry-dip graphite powder process is used, the pollution of flue gas to the environment is reduced, and the influence of secondary casting and porosity on the increase of iron ring resistance is reduced, which creates favorable conditions for the reduction of power consumption of electrolytic aluminum.