The prebaked anode is made of petroleum coke and pitch coke as aggregate and coal tar pitch as binder, and is used as anode material for prebaked aluminum electrolytic cell. This kind of carbon block has been roasted and has a stable geometric shape, so it is also called a pre-baked anode carbon block, and it is also called a carbon anode for aluminum electrolysis. As the "heart" of electrolytic aluminum, its quality directly affects important indicators such as current efficiency, power consumption per ton of electrolytic aluminum, anode carbon consumption, and anode effect frequency, which in turn affects power consumption and carbon emissions.
Prebaked anodes are consumables, and 1 ton of electrolytic aluminum needs to consume 0.49 tons of prebaked anodes.
High quality prebaked anodes can achieve "energy saving and consumption reduction" and "carbon reduction" at the same time, while pre-baked anodes themselves participate in the reflection and release of CO2, and high-end pre-baked anodes can reduce carbon emissions and directly achieve "carbon reduction". The total carbon emission of the prebaked anode preparation process (including raw material preparation) is about 0.92 tons of CO2. Reducing the loss of the prebaked anode can simultaneously reduce the carbon emission at the raw material end.
The quality of prebaked anodes has gradually improved, and the CO2 emission reduction per ton of electrolytic aluminum production has reached 488-635kg/t·Al, accounting for about 4.36%-5.67% of the total carbon emissions in the electrolysis process.
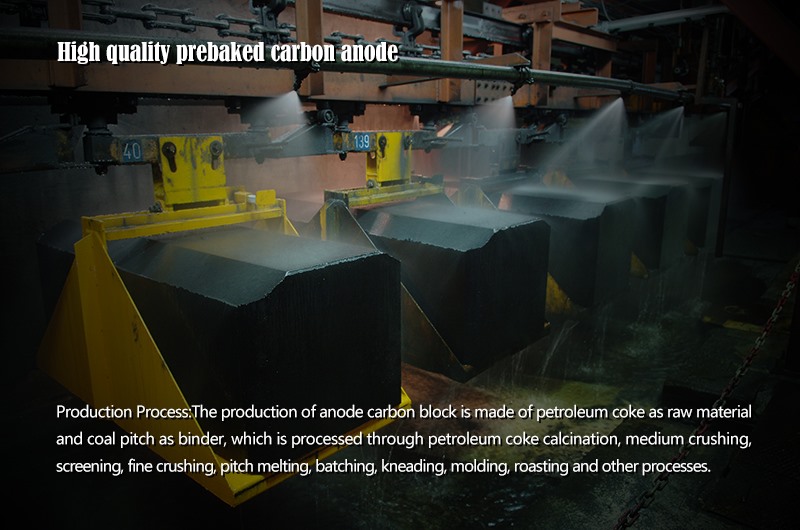
Using of high quality prebaked carbon anode:
The prebaked carbon anode is usually installed on the upper part of the electrolytic cell, and a strong DC current of 60-300ka passes through the carbon anode and introduces the electrolyte. The resistivity of the carbon anode is 50-70 μΩ.m, plus the guide rod and contact resistance, the voltage drop on the consumed carbon anode during normal aluminum electrolysis production is 300-500mV, accounting for 10%-15% of the voltage drop of the electrolytic cell %. At the point where the bottom of the carbon anode contacts the molten electrolyte, a complex electrochemical reaction (anodic reaction) that decomposes alumina occurs. With the participation of carbon, the anode end products are CO and CO2. In the production of aluminum electrolysis, the average daily consumption of carbon anodes is 1-2CM. Regularly adding new anode paste to the upper part of the electrolytic cell (for self-baking anode electrolytic cells) or regularly replacing pre-baked anodes (for pre-baked anode electrolytic cells) is the anode work. The main content to keep the anode continuously working properly.
Production Process of high quality prebaked carbon anode:
The production of anode carbon block is made of petroleum coke as raw material and coal pitch as binder, which is processed through petroleum coke calcination, medium crushing, screening, fine crushing, pitch melting, batching, kneading, molding, roasting and other processes.