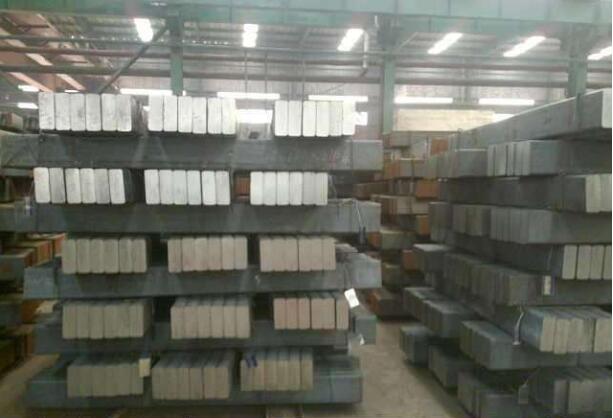
Tons of aluminum dc power consumption =2980X average voltage + current efficiency.Therefore, the only way to reduce the tons of aluminum dc power consumption is to reduce the average voltage and improve current efficiency. At present, the competition in electrolytic aluminum market is becoming increasingly fierce, and reducing energy consumption has become the key factor for the development of aluminum electrolytic production.Due to the damaged cathode carbon block in the overhaul tank, the steel rod was melted, and there was no conductive connector, so it was forced to stop the tank for overhaul. In view of this situation, the electrolytic aluminum cathode aluminum rod was designed.
Electrolytic aluminium cathode rods under the environment of higher than the melting point of 660 ° C were not melting.First, the bottom pressure drop can be reduced, saving tons of aluminum power consumption;The other is to realize that the electrolytic cell will not be forced to stop because the cathode has no conductive rod, thus greatly extending the life of the electrolytic cell, reducing investment, saving cost and increasing efficiency .The third will not affect the quality of the primary aluminum liquid because the original steel rod is melted.