Each pre-baked anode carbon block is composed of three parts: aluminum guide rod, cast steel claw head and pre-baked anode carbon block.They are connected by welding (between guide rod and cast steel claw) and casting of phosphorus pig iron to form the anode carbon block group (Figure 1).The anode carbon block group is generally single block group, there are also double block group and three block group.Each aluminum electrolytic cell is composed of 8 ~ 32 groups of anode carbon blocks.
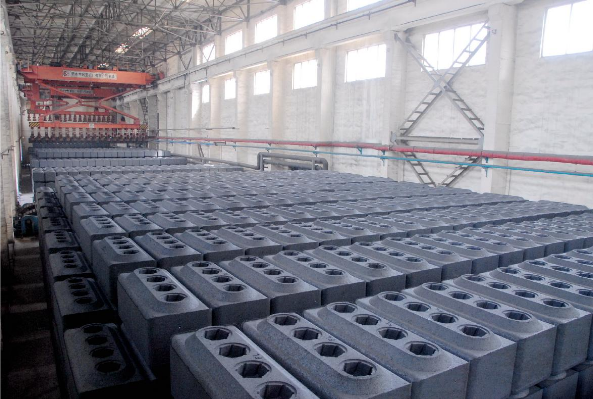
FIG. 1 Anod carbon block assembly for electrolysis
1 - hanging hole;2 -- Anode guide rod;3 - Explosive welding block;4 - Cast steel claws;5 -- Phosphorus pig iron;6 - carbon bowl;7 -- Anode carbon block
The length of the aluminum guide rod is 2000 ~ 2200mm, the cross section is rectangular, the size depends on the current passing through it, and the general current density is 35 ~ 40A/cm2.The cross-sectional area of aluminum guide rod in common use in China is rectangle or square.The conductive surface on the aluminum guide bar contacting with the large horizontal bus shall be processed. It shall be flat and smooth with less oxidation film on the surface to reduce the contact resistance.
Cast steel claw head is cast steel made of ZG25.According to the number of Anod carbon block assembly for electrolysis, the claws have three claws, four claws, six claws. The claws are arranged in a straight line or a rectangular shape. Each carbon block is connected with at least two claws.The aluminum guide rod and the cast steel claw are connected by an aluminum steel explosion welding block (or directly exploding the aluminum rod and the steel claw together).Explosive welding block is a double material combining steel and aluminum by means of detonating explosive. It can realize the transition of steel and aluminum to aluminum welding.This kind of explosive welding block has strong welding, high mechanical strength and small surface contact resistance.The aluminum - aluminum welding between the upper surface of the welding block and the anode guide rod is completed by argon or carbon arc welding, while the steel plate on the lower surface and the steel - steel welding on the top of the cast steel claw are completed by arc welding.Before assembly, the claw head should be sand washed and coated with graphite slurry, which can prevent the erosion of the steel claw head by molten iron, improve the contact state between the steel claw and cast iron, reduce the contact pressure drop, and facilitate the removal of phosphorus and iron during the guide rod cycle.Guide rod and steel claw connector, also referred to as "anode guide rod".The anode rod is recycled during production.After removing the residual group from the electrolytic cell, pressing the dephosphorizing iron ring, straightening the guide rod and sand washing the claw head, and coating the graphite, the residual group can be used to cast the new carbon block group again.
The Anod carbon block assembly for electrolysis has a carbon bowl for the steel claw head.The anode carbon block produced by vibration molding generally has a special device for making carbon bowl on the vibration mold, and the molding and bowl making are completed in one time.The carbon bowl should be processed according to the design requirements before assembling the carbon blocks formed by extrusion.The carbon bowl is round and its depth is generally 80 ~ 120mm.In order to improve the binding force of cast iron and carbon block, the inner wall of the carbon bowl is machined with chute.Generally, there are 6 chute in the carbon bowl, the groove is wedge with upper width and lower width, the groove is 20 ~ 25 mm deep, and the inclination Angle is 70° ~ 75°.